

آخرین مطالب سایت
مطالب تصادفی
محبوبترین مطالب
تبلیغات
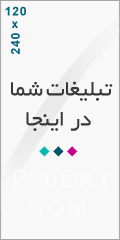
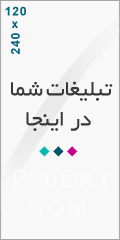
مانیسمان اروپایی
ورق استیل ۳۱۶
ورق استیل سوپر آلیاژی
لوله مانیسمان رومانی
لوله گالوانیزه سپنتا
پیدایش صنعت لوله گالوانیزه و پروفیل فولادی در ایران، در اوایل دهه چهل خورشیدی را باید متقارن با تأسیس شرکت صنعتی سپنتا به عنوان اولین تولید کننده پروفیل در ایران دانست. به گونه ای که نام لوله گالوانیزه سپنتا مترادف و جایگزین نام پروفیل فولادی در آن دوره رواج داشت و تا سالها بعد نیز انواع پروفیل ها را به نام ”سپنتا“ میشناختند. این شرکت در سال ۱۳۳۹ تأسیس و کارخانه تولیدی آن در تهران در سال ۱۳۴۰ به بهره برداری رسید.
گالوانیزه چیست:
گالوانیزه چیست:
برای محافظت از خوردگی و آسیب پذیری فلزات توسط عمل گالوانیزاسیون، پوششی از فلز روی را بر روی این گونه فلزات آسیپ پذیرقرار می دهند این پوشش متشکل از لایه ی روی و ترکیباتی از آهن می باشد. این نوع فلزات کاربرد زیادی در صنعت دارد. (آهن و فولاد)
لوله گالوانیزه:
· ضریب هیزم ویلیام این لوله بر حسب اینچ می باشد
· طول لوله های گالوانیزه شش متر می باشد.
· اتصالات آن قفل ، کمربند و برشن است.
· این لوله ها به وسيله دنده پيچي به يكديگر وصل و توسط مواد مناسب آب بندي مي شوند
لوله های گالوانیزه را می توان به طور کلی به دو دسته عمده بخش بندی کرد
1- لوله های آهنی گالوانیزه:
این لوله ها با رنگ تیره و خاکستریشان است که شناخته می شوند و عموما به دو صورت سبک و متوسط تولید می شوند . جنس این لوله ها از آهن سفید نورد شده می باشد . به این لوله ها ، لوله های با درز نیز می گویند که درز آن توسط دستگاهایی به هم متصل شده و جوش می خورند و در فلز روی مذاب، فرو برده می شود.
مراحل انجام و نکات مهم در عملیات گالوانیزه گرم
گزینش فولاد
انجام یک روکش گالوانیزه دارای مبنای واکنش متالورژی بین فولاد و روی ذوب شده میباشد که منجر به شکل گیری چندین لایه مرکب آهن، روی (برای مثال گاما، دلتا، زتا) میگردد مضافاً از روی ذوب شده به سطح لایههای مرکب میچسبد.
معلوم شده است که ماهیت سازههای واقعی روکش گالوانیزه شده ممکن است بر طبق ماهیت واقعیت شیمایی فولادی که میبایست گالوانیزه شود اصلاح شده باشد، عناصر خاص یافت شده در فولادها معلوم شده است که دارای تأثیر بر روی ساختار روکش میباشد. عناصر کربن از ۲۵٪، فسفر بیش از ۰/۰۴ درصد یا منگنز بیش از ۱/۳ درصد باعث تولید روکشهایی میگردد که متفاوت از روکشهای مشخص شده توسط شکل ۱ میباشد. فولادهای حاوی سیلیکوندر ۰/۰۴ یا ۰/۱۵ یا بالاتر از ۰/۲۲ درصد میتواند نرخهای رشد روکش گالوانیزه شدههایی تولید نمایند که بسیار بالاتر از نرخ آن فولادهایی است که سطح سیلیکون آنها زیر ۰/۰۴ درصد و بین ۰/۱۵ درصد یا بالاتر از ۰/۲۲ درصد میباشد.
مطالعات اخیر نشان داده است که حتی در مواردی که سیلیکون و فسفر به صورت مستقل در حدود مطلوب حفظ شدهاند، نوعاً دارای نمای ظاهری خالداری یا خاکستری تیره میباشد.
تحویل بار
جهت گالوانیزه نمودن قطعاتی که انتهای آنها مسدود شده و امکان جمع شدن مذاب روی در آن مناطق میباشد سوراخهایی جهت تخلیه مذاب تعبیه گردد.
مخازنی که فقط سطح خارج آنها گالوانیزه میشود جهت جلوگیری از انفجار این قطعات در داخل آب مذاب میبایست به لولههایی جهت ورود و خروج هوا هنگام غوطه وری در وان مذاب مجهز شوند که ارتباط فضای داخل مخزن را با فضای بیرون از وان برقرار مینمایند.
در هنگام ساخت پیچ و مهرههایی که به صورت گالوانیزه گرم پوشش داده میشود باید مهرهها را با تلرانس بالاتری ساخت تا به علت افزایش ضخامت پیچ و مهره در اثر قرار گرفتن روی بر سطح آنها هیچگونه مشکلی در هنگام باز و بسته کردن مهره به وجود نیاید.
قطعاتی که باید مورد عملیات گالوانیزه گرم قرار گیرند نباید توسط رنگ روغنی و یا اسپری مارک زنی شوند. این قطعات میبایست از طریق مارکهای سمبهای (حک شدنی) و با مارکهای آویختنی شماره گذاری شوند.
فاصله گذاری
به منظور تماس کامل اسید با سطح فلز لازم است که بین قطعات را به نحوی فاصله ایجاد کرد. سادهترین و مناسبترین روش موجود استفاده از زنجیر است. روشهای دیگر را با توجه به ابعاد قطعه و شکل هندسی آن میتوان به کار برد لازم است ذکر شود که در مجموع قطعات باید به نحوی قرار گیرند که هوا در هیچ قسمتی گیر نیفتد. همچنین در زمانی که از اسید خارج میشوند به راحتی اسید از سطح قطعات تخلیه شود. در صورتی که فاصله گذاری بطور صحیح انجام نشود و قطعات به هم بچسبند در مرحله گالوانیزه کردن محلهای چسبیده به صورت سوختگی نمایان خواهند شد. سنگینی بیش از حد بخصوص در مورد قطعات مسطح باعث میگردد در قسمت تماس زنجیر با قطعه اسید شویی صورت نگیرد وجای آن به صورت سوختگیهای ریز و خطی نمایان شود. در صورتی که قطعات دارای رنگ باشند بهتر است تمام قطعات رنگ دار را جدا کرده ودر یک قسمت از بسکت ودر کنار هم قرار دهیم تا در حین شارژ (شانه گذاری) قطعات سنگ کاری شود.
لازم است ذکر شود که قطعات بزرگ بنا بر شکل هندسی که دارند ممکن به صورت جدا و یکی یکی اسید شویی شوند که احتیاج به فاصله گذاری ندارند، در قطعه دارای هر شکلی وبه هر اندازهای که باشد باید طوری در وان قرار گیرد که اسید به تمام سطوح برسد.
اندازه گذاری لوله های فولادی
اندازه گذاری لوله های فولادی
این لوله و اتصالات از اندازه ۱/۸اینچ تا ۱۲اینچ با قطر اسمی (Nominal Diameter) که حد فاصل قطر داخلی و قطر خارجی می باشد و برای بالای ۱۲اینچ با قطر خارجی (Outside Diameter) مطابق استاندارد ANSI B36.10 مشخص می شود. همیشه برای یک اندازه مشخص با ضخامت های مختلف قطر خارجی ثابت می باشد.
برای مشخص کردن ضخامت لوله ها از سه روش به شرح زیر استفاده می شود:
۱- بر اساس اعلام ضخامت لوله ها به صورت اینچی یا میلیمتری مطابق استاندارد API 5L و یا ANSI B36.10.
۲- بر اساس روش وزنی که به سه دسته استاندارد (STD) و سنگین (XS) و فوق سنگین (XXS) تقسیم می شود.
۳- بر اساس استاندارد ANSI به صورت Sch که از فرمول مقابل بدست می آید SCH=(1000P)/S که Pفشار طراحی (PSI) و S تنش تسلیم (PSI) می باشد.
بین بعضی از روش های فوق روابطی به این شرح وجود دارد:
برای اندازه ۱/۸ اینچ تا ۱۰ اینچ SCH40=STD
برای اندازه ۱/۸ اینچ تا ۱۲ اینچ SCH80=XS
برای لوله های ۱۲ اینچ و بالاتر ضخامت رده STD برابر ۰٫۳۷۵اینچ و برای لوله های ۱۰اینچ و بالاتر ضخامت ردهXS برابر ۰٫۵۵اینچ می باشد.
استاندارد لوله های فولادی ضد زنگ ANSI B36.19 می باشد.
لوله های فولادی مورد استفاده در صنعت نفت و گاز و پتروشیمی
استاندارد ساخت:تست و ابعاد مطابق استاندارد API 5L و یا IPS)M-PI-190) و یا ASTM A106 و یاASTM A53 می باشد.
جنس لوله ها: جنس لوله ها فولاد کربنی می باشد که بر اساس استانداردهای فوق در گریدهایB,X42,X46,X52,X56,X60,X65,X70,X80,… می باشد و بر اساس استاندارد لوله گازی API در دو ردهPSL1و PSL2 می باشد که رده ۱ برای گریدهای بالای X42 منطقه جوش نیاز به عملیات حرارتی دارد و رده ۲ برای همه گریدها نیاز به عملیات حرارتی در منطقه جوش می باشد و فرکانس برق نیز باید۱۰۰KHZ باشد.
ورق استیل چیست
ورق استیل چیست یا ورق استنلس استیل چیست ؟
انواع ورق استیل از نورد شمش های ریختگی استنلس استیل تولید و ساخته میشود که به ضخامت مورد نظر بستگی دارد ، مهمترین ورق استیل موجود در ایران ورق استیل ۳۰۴ تایوان ، ورق استیل ۳۱۶ تایوان ، ورق استیل کره و ورق استیل کلومبوس آفریقای جنوبی میباشد.
قابل ذکر است که ورق استنلس استیل به طور کل در مخازن و دکور بیشترین مصرف را دارد و پس از آن شامل تولید لوله استیل از ورق استیل میباشد . بسته به نوع مصرف انواع ورقهای استیل شامل ورق استیل ۳۰۴ نگیر ، ورق استیل ۲۰۱ نگیر که عمدتا برای مصارف دکوراتیو بکار میرود ، ورق استیل ۳۱۶ که به عنوان ورق ضد اسید شناخته میشود ، ورق استیل ۳۲۱ که ساده ترین نوع ورق نسوز است، ورق استیل ۳۱۰ با درصد بالای کروم و نیکل که تا ۱۲۰۰ درجه سانتیگراد استحکام خود را حفظ مینماید ، ورق استیل ۴۱۰ یا بگیر ، ورق استیل ۴۲۰ بگیر که مخصوص آبکاری میباشد و در ساخت ظروف آشپزخانه کاربرد وسیعی دارد ، ورق استیل ۴۳۰ بگیر که در پوسته و بدنه موتورها و یخچال فریزر و غیره کاربرد دارد و… میباشد. که مهمترین و پر استفاده ترین آنها ورق استیل ۳۰۴ برای مصارف تولید مخزن ، غذایی ، عایق کاری ، و دکور میباشد ، و در رتبه دوم ورق استیل ۳۱۶ میباشد که در صنایع مخازن ضد اسید ، صنایع دارویی جهت جلوگیری از ورود آلایندگی و عدم خوردگی ورقهای استیل ۳۱۶ میباشد . همچنین ورق استیل ۳۲۱ نسوز که در مصارف ضد حرارت و دمای بالا و در کوره ها با دمای نسبتا زیاد استفاده میشود و دمای پایداری در مقابل اکسیداسیون استیل ۳۲۱ تا حدود ۹۵۰ درجه سانتیگراد میباشد . در آخر فروش ورق استیل ۲۰۱ برای مصارف دکوراتیو و تولید لوله نرده بکار میرود . سایر و انواع ورق های استیل در سایزهای مختلف از ۲*۱ ، ۱٫۵*۳ ، ۱٫۲۵*۲٫۵۰ ، ۱٫۵*۶ و ۲*۶ و ضخامت های مختلف از ۰٫۳۵ الی ۵۰ میلیمتر آماده ارائه در سراسر کشور با بهترین قیمت قابل ارائه میباشد .